Auto/Steel Partnership (A/SP) is investigating alternative sustainable joining techniques to resistance spot welding (RSW) for automotive applications. RSW is a mature, high-volume process for joining steel, however the industry is seeking more efficient and sustainable processes with reduced energy requirements. The industry also is interested in joining processes with reduced heat input to mitigate liquid metal embrittlement (LME) in susceptible zinc-coated steels. In a two-phase study, the A/SP Alternative Joining Team evaluated four processes that showed promise in joining advanced high-strength steels (AHSS), third generation AHSS (3rd Gen AHSS), and ultra-high-strength steels (UHSS) for light-weight automotive applications, such as battery electric vehicles. The four processes are:
- Mechanical Clinching (MCL),
- Thermally Assisted Mechanical Clinching (TAC),
- Self-Piercing Rivets (SPR), and
- Thermally Assisted Self-Piercing Rivets (TAR).
The study evaluated the quasi-static mechanical properties and dynamic fatigue properties of the four different technologies applied to twelve (12) different material stack-ups, with and without adhesive, and compared their performance against RSW. The results from the study are summarized in color charts that enable process engineers to easily select suitable manufacturing processes for their respective manufacturing footprints and business models.
The timing and scope of the program did not allow for extensive process development and some material stack-ups could not be effectively joined. These stack-ups were removed from the study, which will show up as a gray square in the color charts.
Phase I: Mechanical Properties Assessment
The mechanical properties were assessed in Phase I of the study using quasi-static tensile testing of lap-shear and cross-tension coupons, with three repeats for each test. Figure 1 summarizes the mechanical property results of the twelve joints with adhesive. Figure 2 summarizes the mechanical property results of the twelve joints without adhesive. The results were normalized against RSW results per the key shown to the bottom-right of the charts.
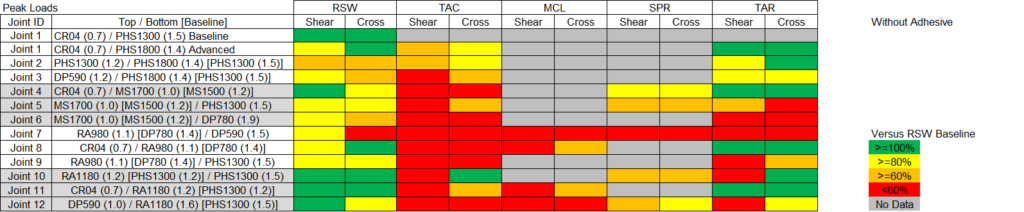
Figure 1: Normalized Mechanical Properties Results without Adhesive

Figure 2: Normalized Mechanical Properties Results with Adhesive
Conclusions and Observations for Phase I:
- Alternative joining can provide improved performance for some material combinations. For example, Figure 3 shows the results for Joint #2, where both TAC and TAR showed improvements in mechanical properties versus RSW:
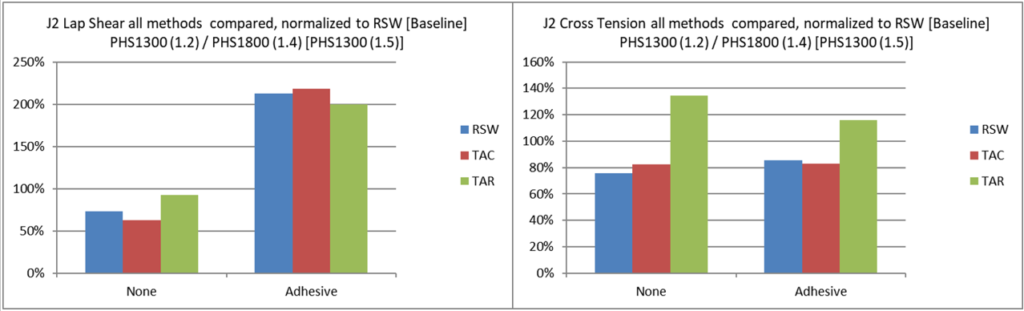
Figure 3: Phase I Lab Shear and Cross Tension results for Joint #2
- The reduction of governing metal thickness (GMT) due to a change to a higher strength steel can have significant effects on joint performance.
Phase II: Fatigue Properties Assessment
The fatigue properties were assessed in Phase II of the study using lap-shear coupons. The SPR process was dropped from the program due to the lack of viable joints in Phase I. Although MCL performance was limited without adhesive in Phase I, it was carried into Phase II testing because of performance with adhesive. The applied load for the fatigue testing was based on a percentage of the tensile properties assessed in Phase I. Five different loads were applied to generate fatigue curves with a 100,000 cycle targets (R=0.1, 20 hZ). Figure 4 shows the results of the fatigue testing, where the results were again normalized against the RSW data.
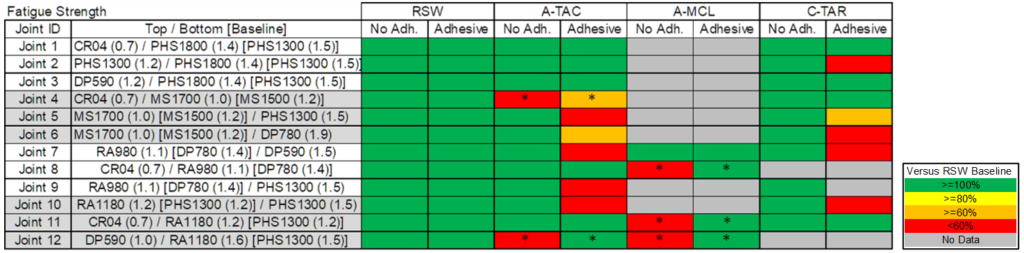
Figure 4: Normalized Fatigue Results
Conclusions and Observations for Phase II:
- Thermally Assisted Clinching (TAC) successfully produced (10) of (12) joints without adhesive. However, only (5) of (12) joints were successfully produced with adhesive.
- Mechanical Clinching (MCL) successfully produced (1) joint without adhesive and (4) with adhesive. However, (3) of the (4) with adhesive were determined to be non-feasible due to excessive scatter.
- Thermally Assisted Self-Piercing Riveting (TAR) was able to successfully produce (10) of (12) joints without adhesive. However, only (4) of (12) could be produced with adhesive.
- As with Phase I, Phase II showed that alternative joining can provide improved performance for some material combinations from both static and dynamic load considerations.
In general, the results without adhesive were better than results with adhesive, which would normally be the opposite of expected results. However, the lack of process development made the joints susceptible to process factors, such as the degradation of the adhesive due to heat, inconsistent or non-uniform application of adhesive. The Team concluded that some of the material combinations with adhesive could be viable with additional process development.
The material configurations were challenging, and sometimes required that material orientation be flipped, e.g. high strength to low strength or visa versa. Again, the lack of process development means that the charts are not a pass/fail criterion for any weld combination, but rather a guide to which weld combinations are current potential candidates for process substitution and the relative performance expectations if converted.
A/SP acknowledges the in-kind support from TOX/PressoTechnik, R&E Engineering Services, Utica International, Atlas Copco, Henrob, and Henkel Corporation.